You probably already have a robust system in place to track the cost of your printing — otherwise you wouldn’t be able to accurately estimate jobs and ensure everything that goes through your shop has a profit margin that keeps the lights on, the equipment running, and your people employed. But are you truly accounting for the entire cost of the project, from start to finish? Specifically, are you accurately tracking the cost of finishing your work?
Tracking costs for entire jobs and on a per-piece basis is critical to ensuring profitability. It’s also an important step when it comes to finding ways to reduce costs throughout your operation without affecting quality or increasing turnaround times. In fact, you might have unexpected and unnecessary costs impacting your bottom line right now, you just don’t know it.
Breaking Down the Cost to Finish
When it comes to ensuring you are pricing your finishing correctly, knowing the exact costs to run every sheet through each piece of equipment is the first step. There are a few things to keep in mind — most of which will be familiar to you if you’ve done this process for your printing devices already.
- The cost of equipment. Just like with your press — be it offset, digital, inkjet, toner, textile, etc. — the first thing to note is the initial investment into the machine and how you are spreading that cost out throughout its lifetime. It doesn’t matter if it’s a large machine that can cut and fold direct mail in the thousands of pieces per hour or a tabletop laminator that requires an operator to run one piece at a time. Make sure you understand the price you need to charge per piece to cover that investment and the supplies used.
- The cost of maintenance. Of course, just like with a press, you can’t put a piece of complex finishing equipment on a pressroom floor and expect it to run flawlessly all day every day without effort. Do you need a maintenance contract or can your operator perform the daily, weekly, or monthly tasks required to keep it running at full speed? Does it require specific materials to maintain, such as washes, to ensure it is clean and running correctly? What about parts or service if something breaks beyond what your staff can handle? Factor all of this into the cost of the machine and make sure your pricing reflects it.
- The cost of labor. Speaking of operators, you may need one or more people who are trained to run your finishing equipment. Depending on the type of equipment and the size of your shop, that might just mean getting your press operator a bit of training, or it might mean hiring additional personnel to run that side of the business. Either way, you’ll want to invest in training to ensure your operators are making the most of the finishing equipment, using it to maximum effect and keeping it in perfect condition to always be ready for the next job.
- The cost of substrates. This might be the one cost you have already considered and it should absolutely be part of the estimating process. While some finishing, such as folding or cutting, don’t require adding anything else to the print job after it leaves the press, others add things like foils, coatings, or lamination — processes that come with their own substrate costs. Make sure you know what you’re spending on them.
- The cost of your time. Finally, how long will that job take to run? Is it a simple cut or fold that can run though the equipment at the fastest rated speeds? Or is it a spot coating job that will need to be carefully run to ensure only the right areas are impacted? When determining your finishing costs, make sure you consider how long each job will tie up the equipment before the next run.
Reducing Job Costs
Now that you have an idea of what the finishing of each job is costing you per piece, let’s find ways to cut down on your job costs.
- Equipment: Is the equipment you are running an older technology that requires a lot of manual processes and skilled labor? Is it breaking down more often that it’s costing you more in downtime and loss of business? If the answer is yes to either of these questions, then maybe it’s time to upgrade to a newer technology that is more efficient and at the end, will reduce touchpoints and increase the profitability of the job. Go through the cost exercise before you buy, to get a rough idea of what you would need to charge for the finishing you’re already doing. If it’s something new you’re adding, how much more revenue can it generate? Can it finish your jobs faster, cheaper, and at a higher quality? Break it all down and see if you are able to save in time and money.
- Maintenance: It might seem counterintuitive to invest in regular maintenance but look at the bigger picture. How much would it cost you if something breaks due to being worn or not maintained correctly? How much would it cost you if you must reprint – and finish again – a job because of faulty equipment? How much would it cost you if the finishing department goes down completely and jobs are left waiting? Spending the time and money for regular maintenance will decrease your overall costs over time.
- Labor: Labor is expensive. Especially now where many are struggling to find people with the right skills, consider investing in automated equipment and workflow automation software. You might have automated quite a bit in your prepress and printing departments, but you likely haven’t done all you can in post-press. Remember, each touchpoint costs money – so, are there tasks you can have automated that will allow you to cut down on labor costs?
- Substrates: There are tons of options out there for every type of finishing substrate — some better than others and some more available. Don’t stop investigating new options as they come to market. Get samples, run them through your equipment, and see how they compare to what you’re currently using. Talk to existing and potential new suppliers and ask if they have a less expensive option you can try that might work just as well. It never hurts to ask. Just don’t skip the step of testing the materials and having a good idea of the pros and cons before you roll something new out to your live jobs.
Taking action to decrease the time and money spent in finishing a job, is going to keep more money in your pockets. With the type of technologies and automation now available in the market, reducing the cost of your print finishing is easier than ever.
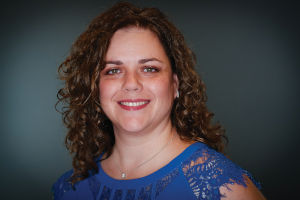
DENISE GUSTAVSON
Guest Blogger
NAPCO Media